Ceiling Insulation Perth regulates the temperature inside your home, reduces noise and saves on energy bills. It also reduces greenhouse gases resulting from power generation and aligns with worldwide initiatives for sustainable construction and operation of buildings.
There are several options for insulating your ceiling, including blown-in products and rigid boards such as EPS or PIR. This article will focus on the benefits of installing ceiling insulation at a new build, as well as in existing homes.
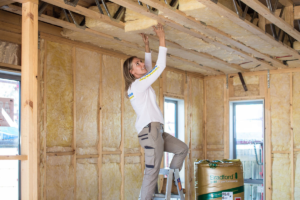
Insulation is one of the most important investments you can make in your home. It not only protects your family from harmful effects of outdoor temperatures, but also helps you save money on energy bills. Choosing the best insulation for your home depends on many factors, including its R-value, which is an industry standard that measures how well a product resists air leakage and heat flow. The higher the R-value, the better the insulation.
The two most popular types of insulation are blown-in and batts. Each has its own set of benefits and drawbacks. However, it is crucial to choose the right insulation type to ensure your home has an optimal R-value and a comfortable environment.
Blown-in insulation consists of loose-fill cellulose or fiberglass material that is blown into walls, attics and other hard-to-reach spaces with a blower. This type of insulation is more expensive than a traditional roll of fiberglass but is highly effective at filling small crevices and gaps, enhancing energy efficiency.
Another benefit of blown-in insulation is that it can easily be installed in new homes before drywall installation. This can prevent a lot of costly construction mistakes, such as not sealing around electrical wiring. Additionally, blown-in insulation can be used in attics and crawl spaces to increase energy efficiency.
When it comes to maintenance, blown-in insulation needs to be regularly checked for moisture and pest damage. This is especially true for older homes, as a lack of proper maintenance can lead to the deterioration of insulating materials. It is also important to keep in mind that if you are considering a DIY installation, it may be best to hire a professional to ensure the job is done correctly.
PIR Boards
PIR insulation is a popular choice within the industry for many clear reasons. It offers a strong level of thermal performance that avoids the passage of heat. In addition, it can be manufactured with foil facings that inhibit the passage of moisture. This makes PIR ideal for use as a continuous vapor barrier that will keep the building’s interior dry and prevent any damp problems.
Foil faced rigid PIR insulation boards provide an effective and cost-effective solution to many different types of insulation requirements for both new build projects and renovations. This type of insulation does not require any special maintenance and is extremely durable. It is also easy to work with, enabling builders to cut the boards to size easily.
This type of insulation can be used for various applications including insulating walls, floors and foundations. However, it is most commonly used for insulating ceilings and roofs in the construction of houses, commercial buildings and industrial properties. These types of insulation are often used in conjunction with a variety of roofing systems such as metal sheeting or timber frame.
Unlike expanded polystyrene (EPS), the foam in PIR insulation is closed-cell and therefore does not absorb water. In turn, this makes it resistant to water absorption and a more resilient insulation option that can resist rot, mold and mildew.
Rigid PIR insulation can be produced in a range of thicknesses from 20mm to 200mm. These thicker PIR insulation products are perfect for achieving minimal U-values and maximising energy efficiency.
PIR insulation does not rot or decompose and it can withstand high levels of humidity. It is also fire-retardant and non-toxic and can help to reduce the risk of mold, fungi and other microorganisms. Typically, PIR insulation has an MDI/polyol index (based on the isocyanate and polyol stoichiometry to produce urethane) of greater than 180, meaning it is a high-performance product. This means that it has a much higher compressive strength than other insulation materials such as mineral wool and offers the ability to carry heavy loads. This is a vital consideration in the construction of both flat and pitched roofs.
Mineral Wool
A long-time favorite, mineral wool is an economical, non-combustible, and sound-absorbing insulation option. It also offers superior energy efficiency compared to fiberglass, with R-values of about 23 for 2×6 walls versus the R-19 offered by fiberglass batts. Plus, it contains up to 70% recycled material. It retains its shape better than fiberglass or cellulose, and moisture won’t compromise or degrade its thermal performance. It’s also termite-resistant and does not provide food for microorganisms.
Mineral wool insulation includes spun yarns that are made of melted glass or stone, combined in a certain way, and then pressed into boards or batts that function as insulation. Because it’s so dense, it resists air movement and is a good choice for insulating floors, walls, and ceilings to reduce sound transmission. It is also highly effective in blocking the flow of heat from one area to another.
In addition, unlike spray foam, it is inherently fire resistant and will not melt. When paired with special fire-rated sheathing, it can be used to achieve a one-hour fire rated assembly without the need for expensive furring.
Another advantage of mineral wool is that it’s much easier to cut than fiberglass, allowing you to precisely fit insulation around windows and doors. This is particularly helpful in older homes where framing and wall thicknesses vary. It’s a good choice for insulating ceilings in vaulted rooms where it can help with soundproofing as well as reducing energy costs.
Johns Manville’s ROCKWOOL® stone wool is a non-combustible material that consists of inorganic fibers derived from basalt, a volcanic rock. This wool has a high fiber density and low shot content to ensure maximum energy efficiency and performance. It is available in a variety of R-values to match the requirements of any building. It also carries a Euroclass A1 rating and can be used in combination with fire-rated sheathing to create a one-hour fire-rated assembly. The product can also be perforated, cut, or adjusted on-site without losing its fire resistance. It is also exempt from Germany’s chemical ban ordinance as long as it meets the three compliance exoneration certificate criteria.
Phenolic Boards
Phenolic boards are a highly effective type of rigid insulation for walls, floors and roofs. Their low lambda value, at 0.018 W/mK, makes them up to 50% more efficient than many of the other insulation materials currently available on the market. They are ideal for use in older buildings with constrained space for insulation, as they can be installed in a variety of wall and floor build ups.
They are also highly resistant to moisture, so they’re an excellent choice for areas of the building that receive a lot of rain and condensation. Additionally, they are extremely fire-resistant and won’t rot or develop fungus. The only downside to this kind of insulation is that it can be somewhat fragile, so it’s best used in areas of the home or office where it won’t be subjected to a lot of physical stress or impact.
Rigid phenolic insulation boards are manufactured using a combination of phenolic resins and cellulose fibres, which are then compressed under high pressure. This process results in the production of a dense, closed-cell insulation that has good thermal and sound insulating properties. A range of different facings can then be added to the boards, including aluminium foil and glass tissue. Depending on the application, other materials such as expanded polystyrene (EPS) and cork can also be added to the board.
The phenolic board manufacturing process also produces no CFCs or HCFCs, which helps reduce environmental impact. The blowing agent is typically pentane or another hydrocarbon with similar properties, and the boards are faced with gas tight aluminium foil or glass tissue to help prevent escape of this material during the manufacture of the insulation.
Like other insulation products, phenolic boards must be properly installed in order to optimise their performance. It’s important to ensure that the surface where the insulation is going is clean, dry and free from dirt. It’s also crucial to ensure that the correct thickness is selected. Too thin and the insulation won’t be as effective, too thick and the boards can become brittle or break down over time. It’s also worth bearing in mind that regular inspections of the insulation are vital, as these can help identify any potential problems before they develop, and they’ll allow any issues to be addressed promptly.